Catalytic Plate Reactors
Supplying heat directly into
an endothermic reaction, rather than via
inter-stage heaters or by radiation to a packed
tube is a vital key to intensifying many
important chemical processes. The catalytic
plate reactor (CPR) offers an attractive route
for achieving this. In a CPR, metal plates
coated with a suitable catalyst are arranged in
such a manner that exothermic and endothermic
reactions take place in alternate channels (Fig.
1). These channels typically have a height of
order of millimetres and a catalyst thickness of
the order of microns.
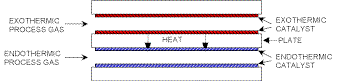
Fig. 1 - A pair of adjacent channels in
the catalytic plate reactor
The research work at the
Process Intensification Group of Newcastle
University has focused on the development of a
detailed theoretical study on CPR's with the aim
of providing a base line for a general design
procedure. The advantages of CPR designs over
conventional reactors arise due to excellent
heat transfer characteristics and minimal
intra-catalyst diffusion resistance. The heat
transfer mechanism within a CPR is via
conduction through the plates separating
alternate process channels and as such is
largely independent of the process gas
superficial velocity. The catalyst layers within
a CPR are thin which results in minimal
diffusion limitations and thus high catalyst
utilisation. These advantages result in reactors
which are smaller, lighter and with a small
associated pressure drop than conventional
alternatives. The potential saving in reactor
volume can be seen in Table 1, below:
Table 1 - Size reduction through CPR
utilisation
|
Reaction |
Current
Technology |
Size
Reduction Factor |
|
|
Steam Reforming |
Packed Tubes in
Furnance |
>100 |
|
|
Fischer Tropsch
Synthesis |
Slurry Bed
Reactor |
4 |
|
Catalytic Steam Reformer
The feasibility of the concept
of coupled endo and exothermic reactions has
been demonstrated using steam reforming of
methane as the fast and highly endothermic
reaction with the energy being provided by the
catalytic oxidation of methane. Potential
exploitation of this system includes on-board
hydrogen production for fuel cell powered
vehicles, which are of particular interest due
to stringent legislation for the control of
automobile exhaust gases. This is possible due
to the significant size reduction (see Table
1). Another important application is the
production of syngas, which is the feed-stock
for many industrial processes. Methods for
preparing and coating the catalysts (based on
sol-gel technology) have been developed and the
necessary activity to achieve a targeted heat
flux of 10kW/m2 demonstrated.
The replacement of the
homogeneous combustion used in conventional
reactors by the catalytic one brings several
advantages. It proceeds at lower temperature
than conventional combustion, posing fewer
constraints for materials of construction and
producing virtually no NOx. Since it is a
flameless process, long radiation paths needed
in conventional fired furnaces are replaced by
channel dimensions of one or two mm, with an
obvious impact on reactor size.
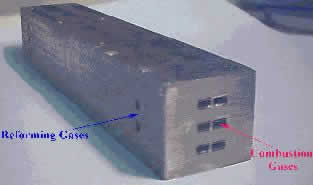
Fig. 2 - Design of simple
CPR by using stacked diffusion bonded shims
(manufactured by Chart Exchangers)
An example of the reactor
design where methane combustion and reforming
are integrated is shown in Fig. 2. The device
used in experimental work is shown in Fig. 3.
These devices are produced from patterned metal
shims which are stacked together and diffusion
bonded yielding a compact metal block.
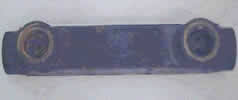
Fig. 3 - Bench scale CPR
for methane steam reforming
An additional important
benefit of this concept is that the production
scaling can be handled through replication
rather than re-sizing. This leaves the reactor
performance effectively the same at all scales,
thus reducing the time requirement from
development to commercial production.
Methane Reforming in a
Catalytic Plate Reactors
The potential of the CPR for
dry or mixed reforming is currently being
investigated. In the process methane, steam and
carbon dioxide are simultaneously passed over a
nickel based catalyst. The technique has been
shown to strongly influence both the the CO:H2
ratio and rate of carbon laydown. A parametric
study is underway in an effort to minimise coke
deposition whilst producing a CO/H2 ratio which
is suitable as a feedstock for Methanol or
Fischer Tropsch processes.
Fischer-Tropsch synthesis in a
CPR
A second application of the
CPR is product enhancement for catalytic
reactions where the product spectrum is highly
dependant upon catalyst temperature. In such an
application alternate channels contain a boiling
heat transfer fluid to maintain an isothermal
catalyst temperature. To demonstrate the concept
the Fischer-Tropsch (FT) reaction has been
investigated.
The hydrocarbon product
spectrum produced by a FT catalyst is highly
dependant upon catalyst temperature and rate of
diffusion of reactants into the catalyst matrix.
The reaction is highly exothermic and if rates
of heat removal from the catalyst are not
sufficiently high "hot-spots" will form which
will result in degradation of the product
spectrum. Studies have revealed that thin
catalyst coats attached to heat transfer surface
areas within a CPR can greatly enhance the yield
of desirable products per unit volume as
compared to conventional fixed bed technology.
This volume saving coupled with an overall
lighter design, requiring less ancillary
equipment and with a low pressure drop make the
FT CPR a potential reactor for the recovery of
stranded gas reserves.
|