Adipic Acid Crystallisation
using A spinning Disc Reactor (SDR)
Introduction
The spinning disc reactor (SDR)
technology is based on the surface rotation
technique and is aimed at intensifying rates of
processes which present heat and mass transfer
limitations in conventional processing equipment
[1]. The creation of high acceleration
fields by rotation causes reacting fluids
introduced on the surface to flow in the form of
thin, intensely mixed films. The thin‑film
characteristics of the SDR fulfil the major
requirements of an ideal reactor: excellent heat
transfer, mass transfer and mixing
characteristics even in quite viscous reaction
media. Apart from utilisation of polymerisation
[2] and chemical reactions [3], SDR Technology
can be applied to control particle size in
crystallisation [4], including nanoparticle
formation. Applications in which the solid
content of a process fluid often poses a number
of problems with regard to fouling in
conventional devices, can be handled by the
rotating equipment. The rotating action in
itself provides a scraping or ‘self‑cleaning’
mechanism strong enough to shift any solid
deposit away from the surface of revolution,
thereby ensuring maximum exposed area at all
times during operation [5].
Crystallisation experiments
were performed in a SDR using adipic acid (HO2C‑(CH2)4‑CO2H;
hexanedioic acid or 1,4‑butanedicarboxylic acid)
which is a valuable intermediate in a wide range
of applications, including the following:
-
As a monomer
in nylon, paper additives,
copolyamides, terpolymers and
unsaturated polyester resins
(UPRs);
-
In polymer
additives for epoxy curing
agents and plasticizers;
-
As a chemical
intermediate in synthesis;
-
In other
applications such as solvents,
lubricants, electronics, soil
conditioners, glass protection
agents, briquetting agents,
leather tanning agents, food
additives and cleaning aids.
Adipic acid was originally
made for the production of nylon, but is now
increasingly used in a wide array of industries
for a broad range of applications and is
currently a key raw material of polyamides and
polyurethanes.
The crystals produced through
a crystallisation process have a critical
influence on the downstream processing.
For that reason, the particle size distribution
(PSD) should be reproducible in each operation
and as regular as possible. It is
therefore very important that the variables that
affect the crystallisation process be known and
easily controlled, in order to satisfy the
requirements concerning the final product
quality and the production demand. The
main purpose of this investigation is to propose
and analyse ways to improve the performance of
adipic acid crystallisation processes.
Experimental Results
Cooling crystallisation
Solutions of adipic acid in
water at range of temperatures (30 ‑ 600C) were
transferred onto a spinning disc reactor, with
the disc surface temperature kept at 200C.
The solution temperature was kept constant
before the liquid hit the surface, to prevent
crystallisation to occur before the disc stage,
by dipping the delivery tube in a constant
temperature (coinciding with the temperature of
the solution) water bath (Figure 1). After
being processed in the SDR, the crystals were
filtered, dried and analysed for PSD, using
Malvern Mastersizer S. Furthermore, all
samples were analysed using Scanning Electron
Microscopy (SEM). Solubility diagram of adipic
acid in water is presented in Figure 2 (a) [6].
Figure 2 (b) presents solubility diagrams of adipic acid in various solvents.
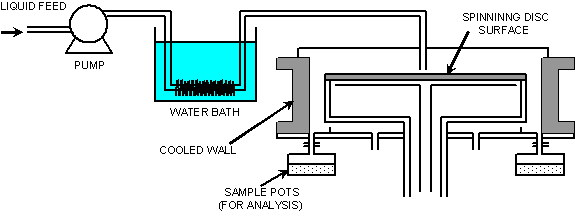
Fig. 1 - Experimental set up
(a) |
(b) |
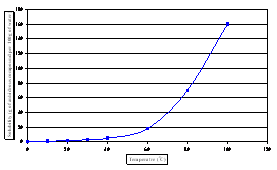 |
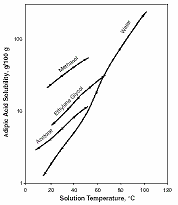 |
Fig. 2 -
Solubility
diagrams for
adipic acid; (a)
in water, (b) in
various solvents
[7] |
Parameters varied in this
study were: adipic acid solution temperature
(ranging from 300C to 600C), liquid solution
flow rate (ranging from 130 cm3/min to 540
cm3/min) and disc rotational speed (ranging from
500 to 2500 rpm).
SEM images of adipic acid
before re‑crystallisation can be seen in Figures
3 (a) and 3 (b). Supersaturation ratios
were kept at 1.89 (for the 600C solution) and
1.62 (for 400C solution).
(a) |
(b) |
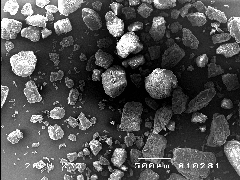 |
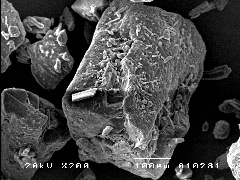 |
Fig. 3 -
Adipic
acid crystals
before
re-crystallisation;
(a)
Magnification:
50x, (b)
Magnification:
200x |

Fig. 4 - PSD trends compared to
starting material
Comparison between adipic acid
crystals before and after processing on the SDR
is shown in Figure 4 and sample SEM images for
the product of disc run performed at 2500 rpm
and 200 cm3/min are presented in Figure 5.
(a) |
(b) |
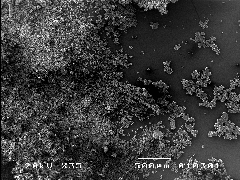 |
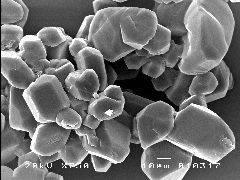 |
Fig. 5 -
Disc speed: 2500
rpm, flow rate:
200 cm3/min;
(a)
Magnification:
35x, (b)
Magnification:
750x |
Anti-solvent
crystallisation
Anti-solvent crystallisation
(or drown out crystallisation), widely used in
the pharmaceutical industry, was accomplished by
adding a miscible anti-solvent into a mixture of
solute and solvent, effectively reducing the
original solubility of the solute in the
solvent, increasing the supersaturation and
thus, causing the crystallisation of the solute.
Anti-solvent used must be
miscible/partially miscible with the original
solvent over the ranges of concentrations
encountered, and the solute must be relatively
insoluble in it. Additionally, the final
solvent/anti-solvent mixture must be readily
separable.
Systems used in this study
included various alcohols (solvent)/ethyl
acetate (anti‑solvent), THF/ethyl acetate,
acetone/ethyl acetate, alcohols/water,
THF/water, acetone/water, however,
crystallisation on the SDR did not happen except
in cases of isopropanol/water where some
crystals were observed and ethanol/ethyl acetate
where more adequate results were accomplished.
The results for ethanol/ethyl
acetate are presented in Figures 6 and 7 for
different flow rate ratios between streams of
solvent (ethanol) and anti‑solvent and various
disc rotational speeds. It can be seen (in
Figure 6) that, as far as the particle size is
concerned, ratio between flow rates is very
important and having more solvent in the system
reduces the average crystal size down to 5 mm.
Disc rotational speeds did not have as much
influence, nevertheless a shift towards larger
size crystals can be easily distinguished with
the decrease of rotation speed (Figure 7).
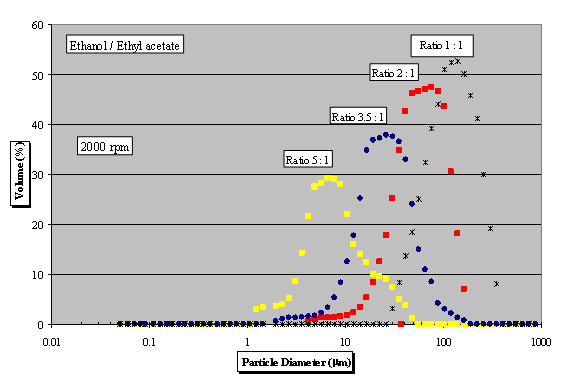
Fig. 6 - PSD using
anti-solvent crystallisation for various flow
rate ratios between solvent and anti-solvent at
2000 rpm
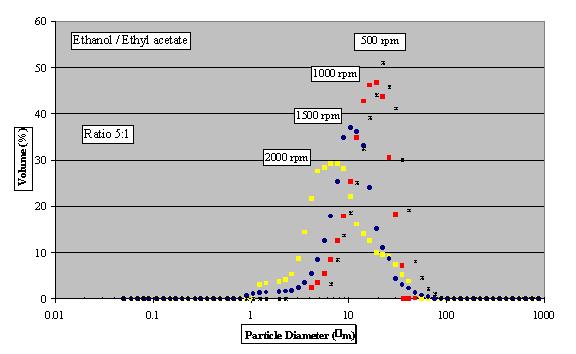
Fig. 7 - PSD using anti-solvent
crystallisation for various disc rotational
speeds with solvent/anti-solvent flow rate ratio
of 5:1
Conclusions
Adipic acid crystallisation
experiments performed in a spinning disc reactor
by cooling crystallisation have shown that
crystal size and PSD can be easily controlled by
adjusting parameters such as supersaturation
ratio, disc rotational speed and liquid flow
rate.
Drown out crystallisation was
also tried in a SDR using various systems, but
viable results were only obtained using
ethanol/ethyl acetate system. From the
obtained results it was obvious that the size of
the crystals was extremely dependent on the
ratio between the streams of solvent and anti‑solvent.
Using these crystallisation
techniques, average particle sizes of around 15
mm were obtained in the SDR and the range of
particles from less than a micron to around 70
mm were attained by varying the experimental
conditions (supersaturation, disc rotational
speed, feed flow rate).
|