The production of polymer
nanocomposites using intensified modules
The advent of a new
generation of polymer nanocomposites in recent
years has resulted in the emergence of
substantially improved engineering and
structural materials with enhanced mechanical
properties. Such materials comprise a wide range
of conventional homopolymers and filler
materials such as treated clays, inorganic
particulates, carbon nanotubes and glass fibres.
To date, the focus of much of the literature has
been on the conception and testing of new
nanocomposites and their properties,
particularly clay-based systems, and to a lesser
extent particulates. However an efficient,
continuous method of generating such materials
has yet to be developed.
Process Intensification,
(PI), is a strategy which entails the reduction
of process volume without a decrease in product
throughput. Its aim is to enhance mixing and
improve mass and heat transfer rates and so
optimise the conditions for effective chemical
reactions. This should result in improved
conversion and product quality, as well as
reducing waste through improved selectivity.
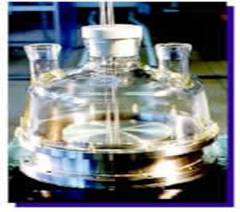
Fig. 1 -
Spinning Disc
Reactor |
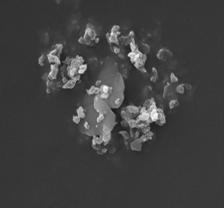
Fig. 2 - Barium
Sulphate
Crystals (0.2 -
0.7 mm) |
PI offers the potential to
produce particulate-based nanocomposites in a
continuous mode which optimises the necessary
conditions for the three key processes of
polymerisation, nanoparticle production and the
effective mixing of the two composite elements
of particle and polymer.
The Spinning Disc Reactor,
SDR (Figure 1), has been employed for the
synthesis of poly(methyl-methacrylate) by means
of photo-initiation under ultra-violet light at
25°C. It can be operated as a one-pass reactor
or used to recycle a polymerising mixture until
the desired mass yield and molecular weight
properties have been achieved. The aqueous
production of particles to sizes of the order
0.1- 0.7 mm, (Figure 2), has also been indicated
on SDR and spinning cone devices suggesting the
possibility of an integrated reaction and mixing
process where polymer and particle can be
generated and inter-dispersed simultaneously.
The development of such a process is the primary
objective of this project.
The project has been in
progress since November 2002 and is due for
completion in February 2006. The principal
sponsors are Protensive Ltd. and the Engineering
Physical Sciences Research Council, (EPSRC).
Additional collaborators include Drs. K.V.K.
Boodhoo, (supervisor) and W.A. Dunk, (Protensive
Ltd., Newcastle).
For more information please
contact Dr Kamelia
Boodhoo.
|