Microreactors
Improved methods of
manufacturing at the micro scale are opening up
new avenues for the development of compact
devices for functions ranging from reactions to
extraction and separation. Much of the initial
work in this field has concentrated on the
development of systems using single phase flow
with diffusive transfer between parallel
reacting fluid streams.
Work within our department has
however focused on the more complex system of
multiphase flow in narrow channels and in
particular immiscible liquid-liquid processes.
The main method adopted to perform multiphase
reactions is the use of slug flow to allow both
convective and diffusive processes to operate
within the reactor channel. An illustration of
the mechanisms involved is provided in the
diagram below.
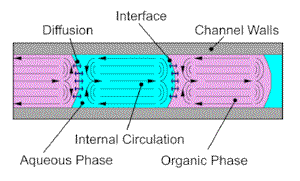
Circulation
patterns within slug flow provide high mass
transfer performance between phases
Generation of Slug Flow
Slug generation within glass
or polymer based on-chip style reactors is
generally achieved by the continuous pumping of
both phases into a “T” or “X” channel
configuration. The photograph below shows the
generation of slug flow for a two-phase
oil-water experiment being performed on a glass
chip with 0.38mm wide/deep channels.
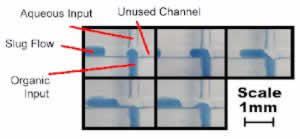
Reaction Visualisation
Flow visualisation of reaction
and mass transfer between slugs was performed as
part of the on-going modelling of slug flow.
A titration process involving
acetic acid transfer from kerosene into an
aqueous solution of NaOH and KOH was used to
visualise the mass transfer. This triggers a
colour change in a pH indicator as show in the
photograph below. In this example the aqueous
slug turns completely yellow after at least 50%
of the acetic acid has transferred, which in
this case occurred after 3.6s.
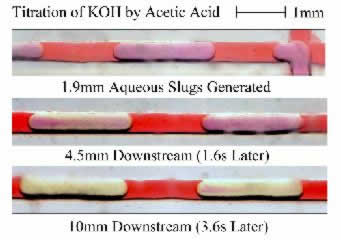
Use of Slug Flow for Chemical
Production
Experiments using slug flow
reactors were also performed for the
industrially relevant process of organic
nitration. A PTFE capillary tube reactor was
used with slug flow generated by use of a
modified tee as shown here.
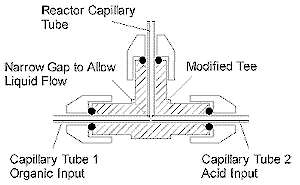
Images of slug flow generated
by this device using a dyed organic phase are
shown in the photograph below. In this system a
0.15mm internal diameter PTFE tube was used to
carry the slugs.

Results
from Benzene and Toluene nitration shown that
slug flow could be used to provide significant
conversion to nitrobenzene and nitrotoluene in
seconds using coiled PTFE reactors of 30cm to
180cm length and compared favourably with
industrial processes.
|