Polymer Film Compact Heat
Exchangers (PFCHEs)
The Process Intensification
Group at Newcastle University has developed a
novel concept of thin film polymer heat
exchangers that offer high thermal efficiency,
reduced fouling, significant reduction in weight
and cost, resistance to chemically aggressive
fluids and the ability to handle both liquids
and gases (single and two phase duties). This
provides PFCHEs, a competitive edge to their
metal counterparts.
The units are of compact
construction and can be of square or spiral
configuration. An important feature of the heat
exchangers that sets them apart from those on
the current market, is the use in some variants,
of a high temperature polymer, poly ether ether
ketone (PEEK). PEEK has a continuous use
temperature of up to 220°C. Although the thermal
conductivity of the polymer is not as high as
metals, the PFCHE made of 100 micron thick PEEK
films offers negligible thermal resistance when
the heat transfer coefficient is less than 4000
W/m2K.
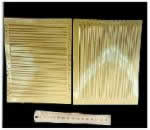 |
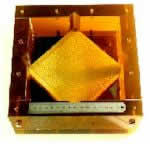 |
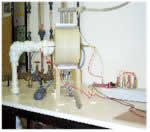 |
Corrugated
PEEK Sheets |
Square PFCHE |
Spiral PFCHE |
The potential market
opportunities are very wide ranging and include
applications in the chemicals and food and drink
industries, with possible applications in
generic equipment such as condensing boilers and
refrigeration plants. There are also
opportunities in the aviation, fuel cell and
automobile industries in the form of cabin air
coolers, filter coolers and radiators. Case
studies on the PFCHEs as a metal alternative in
the aviation and fuel cell industries have been
carried out using heat transfer and pressure
drop correlations developed from different fluid
systems. The fluid systems investigated are
air/air, water/water and glycerol water
mixtures/water for the square PFCHE whilst a
water/air system was studied for the spiral
PFCHE. The results are very positive as it
involves huge cost and energy savings.
Studies on the effects of the
corrugation angle and Prandtl number on the
performance of the PFCHEs are also underway.
Bonding issues have been addressed and among
methods suggested are laser welding,
co-extruding using different materials and using
epoxy fillers/ thin sheets with screen printing.
The issues of cheaper and more cost effective
means of handling the heat exchanger polymer
film are also being looked into.
With these benefits, it is
hoped that, at a later stage, useful heat
transfer and pressure drop correlations
developed for different fluid systems obtained
involving different PFCHE configurations over a
range of Reynolds numbers would enable
alternative compact industrial designs to be
realised.
Table 1 below, shows a
performance comparison of PFCHE with
conventional metal heat exchangers for an
air/air system using the heat transferred per
unit matrix volume. It clearly shows that the
PFCHE has a much higher heat transfer capacity
than conventional metal units and highlights the
advantage of the extreme compactness of the
PFCHE.
Table 1 - Heat Transfer
per Unit Matrix Volume (Air/Air)
|
Type |
Z (MW/m3) for ΔT
= 5°C |
|
|
Serrated Fin
(SF) |
0.60 |
|
|
Wavy-Fin (WF) |
0.27 |
|
|
Flat Tubes (FT) |
0.16 |
|
|
PFCHE |
1.09 |
|
|