Spinning Disc Reactor for
Intensified Polymerisation Processes
It is believed that the
reactors of the future will operate under
continuous as opposed to the traditional batch
mode and will be capable of achieving heat and
mass transfer rates higher by orders of
magnitude than the conventional batch reactors.
More importantly the reactors will provide the
ideal fluid dynamics environment for optimising
product quality, reducing reaction times and
enhancing selectivity.
At the Process Intensification
and Innovation Centre (PIIC) in Newcastle
University, ongoing research is exploiting the
opportunity offered by thin highly sheared and
unstable films (Figure 1) in their application
to polymerisation processes. The thin films are
continuously produced on rotating surface of a
Spinning Disc Reactor (SDR) under the action of
large centrifugal forces which cause the films
to be thrown off the disc at very large
velocities. Extensive heat and mass transfer
studies have shown that convective heat transfer
coefficients as high as 14 kW/m2K can be
achieved in the SDR giving overall heat transfer
coefficients as high as 5–7 kW/m2K. Such
enhanced heat transfer characteristics make the
SDR an ideal system for performing highly
exothermic reactions as good control of reaction
exotherms can be achieved even with the use of
higher feed concentrations.
One class of highly exothermic
reactions which have been studied in the SDR is
polymerisation reactions. Conventional polymer
reactor technology include large stirred tanks
and unagitated towers in batch or continuous
mode. These have serious limitations especially
at high conversions. Heat removal combined with
poor mixing levels in high viscosity/high
polymer concentration mixtures result in poor
control of reaction temperature. The occurrence
of "hot spots" and "temperature peaking" results
in a broadening of the molecular weight
distribution (MWD) and hence poor polymer
product quality. In practice, the operating
temperature and hence the rate of polymerisation
also have to be restricted to prevent thermal
runaways.
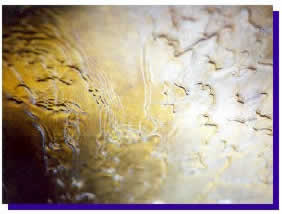 |
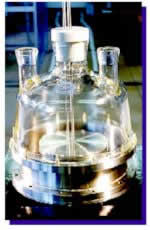 |
Fig. 1 -
View of surface
waves on a
smooth rotating
disc |
Fig. 2 -
Internally
cooled Spinning
Disc Reactor |
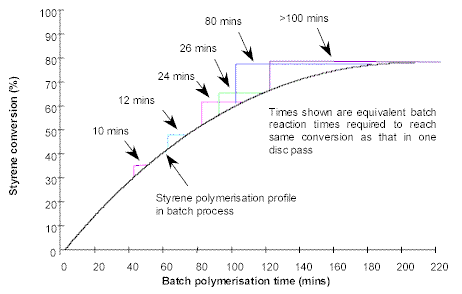
Fig. 3 - Free-radical
polymerisation of styrene at 90°C
initiated by BPO in batch and SDR
Faster
rates of thermally initiated free-radical
polymerisation of styrene are achieved on a 360
mm diameter grooved disc at 90°C and rotating at
850 rpm than in a conventional batch reactor.
Processing times can be reduced in the SDR by as
much as 80 to 100 minutes in one disc pass in
the high conversion region (Figure 3). Also,
good control of molecular weights and molecular
weight distribution (MWD) is possible in the SDR
as a result of enhanced heat transfer and mixing
levels even at high viscosities of the
polymerising system. An EPSRC funded project is
currently looking at the fundamental kinetics
and mechanistic aspects of styrene
polymerisation in the SDR, which is being
carried out in collaboration with the Centre for
Polymer Science at Sheffield University led by
Prof. Ebdon.
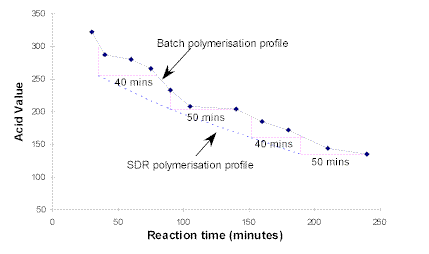
Fig. 4 - Step-growth
polymerisation of maleic anhydride and ethylene
glycol at 200°C
in batch and SDR
The rate
of condensation polymerisations is controlled by
the rate of removal of a small by-product
molecule, usually water or alcohol from the
polymerising system. The diffusion process is
slow in a very viscous melt contained in a large
batch reactor. Significant reductions in
reaction times are achieved in the Spinning Disc
Reactor in the low acid value region for the
unsaturated polyesterification reaction between
maleic anhydride and ethylene glycol at 200°C
and disc speed of 1000 rpm.
At high viscosities (or low
acid values), it appears that the diffusion
control limitations imposed by the bulk viscous
reaction mixture in the batch reactor system are
easily overcome in the thin film formed on the
rotating disc surface enabling the
polymerisation to proceed in the SDR at its
inherently faster rate.
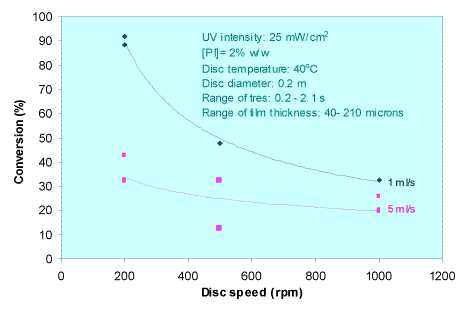
Fig. 5 -
Photopolymerisation of n-butyl acrylate in SDR
Radiation induced
polymerisations have very rapid rates of
initiation but the major limitation is that the
reaction system has to be in the form of a thin
film for efficient penetration of the UV
radiation. The thin film characteristics offered
by the Spinning Disc Reactor make it an ideal
reactor for continuous photo-polymerisation
processes. For the UV-initiated free-radical
polymerisation of n-butyl acrylate, conversions
as high as 90%, with average molecular weights
Mw in the range 58,000 to 70,000 and
polydispersity indices in the range 1.8-2.0,
have been achieved at a residence time of less
than 3 seconds on a smooth rotating disc of 200
mm diameter. Interestingly, branching effects,
which make bulk polymerisation of acrylates
difficult in conventional reactors, were absent
in the SDR polymer product. The flow
characteristics in the SDR clearly suppress any
transfer reaction in the polymerising film and
thus result in an entirely linear polymer.
Currently, the merits of
polymerising styrene in the SDR by
photo-initiation and using solid Lewis acid
catalysts for cationic polymerisation are being
explored in a joint collaboration with the Green
Chemistry Group at York University funded by
EPSRC under the programme of Collaboration
between Chemists and Chemical Engineers.
|