Production of Nano-particles
on the SDR
The Process Intensification
and Innovation Centre (PIIC) at Newcastle
University has pioneered a process for
continuous production of nano particles using
thin highly sheared films which can be generated
on a rotating surface. Unsteady film surface
waves coupled with the shearing action of the
rotating surface ensure that micro mixing is
achieved on the disc. These films are less than
100 microns thick and so offer a short diffusion
path length resulting in excellent heat and mass
transfer performance. Residence times on the
Spinning Disc Reactor (SDR) range from a few
seconds down to fractions of a second. Therefore
the SDR is well suited to fast processes where
the inherent reaction kinetics are of the same
order or faster than the mixing kinetics.
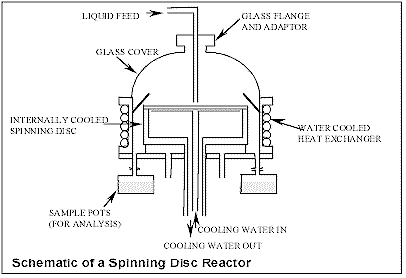
Several reactive
crystallisation pathways have been studied to
exploit the intense mixing conditions on the
disc. Highly supersaturated homogeneous
solutions can been created on the disc, leading
to homogeneously nucleated nanoparticles. Among
others, the precipitation of barium sulphate
from barium chloride and sodium sulphate has
been investigated. It was found that uniformly
distributed nanoparticles could be produced an
order of magnitude smaller than those crystals
formed in an agitated batch vessel as is shown
in the graph below. These particles have
applications in many industry sectors such as
paints/pigments, electronics and
pharmaceuticals.
As well as liquid/liquid
reactions, gas/liquid reactions can also be
carried out on the SDR. An atmosphere of carbon
dioxide diffusing into a thin film of calcium
hydroxide enabled nanoparticles of calcium
carbonate to be precipitated. Titanium dioxide
nanoparticles have also been precipitated on the
disc.
Extended projects have
included the use of ultrasound to influence
precipitation's, and the use of surfactants to
arrest crystal growth.
The graph below shows crystal
size distributions for barium sulphate produced
on a modified SDR. The two SDR curves
representing two reactant feed rates compare
favourably with the equivalent batch result. The
crystals formed from the SDR are an order of
magnitude smaller than those formed in the batch
reactor and are held within a tighter size band.
These results are reproducible and work is
underway to tailor crystal size and distribution
using several operating parameters.
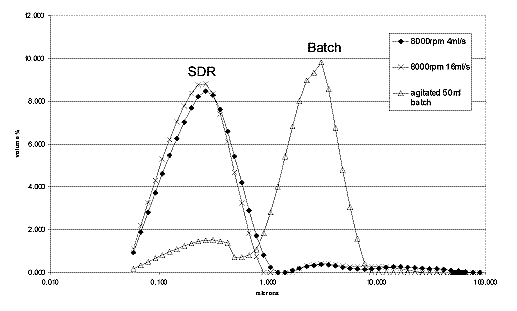
|